![]() | ![]() | ![]() | ![]() | ![]() |
---|
ProX SLS 6100
PRODUCTION-READY FOR TOUGH, FUNCTIONAL NYLON PARTS
Production-grade nylon materials, advanced software workflow and new Selective Laser Sintering technology come together for a versatile solution for functional prototyping and direct 3D production with accuracy, durability, repeatability and lower total cost of operations.
Economically manufacture injection molding-grade plastic parts for demanding end-use and functional prototyping applications. The ProX SLS 500 takes the original SLS (Selective Laser Sintering) technology to the manufacturing floor. This production system produces ready-to-use functional parts and complete assemblies for a variety of uses in aerospace, automotive, patient-specific medical devices, production tooling and manufacturing applications – without time- and cost- intensive tooling or CNC programming.
Unmatched part quality with uniform properties
In tandem with DuraForm ProX plastic material, the ProX SLS 500 produces a part quality previously unknown for SLS. DuraForm ProX plastic materials have been optimized, validated and tested to ensure uniform part properties, high resolution, edge definition and smooth surface finish. Our customers compare it to injection-molding part quality.
Manufacturing economics
Of every kilogram of material used in a build on the ProX SLS 500, up to 95% (950 grams) is turned into parts. This excellent recyclability and efficiency results in comparably lower part costs. With its automated production tools, powder handling and recycling functions, and mobile production controls, this production printer allow you to streamline your workflow and accelerate your time to part. Production rates are up to 7 times faster than comparable technologies.
Production-Grade Nylon
With a range of production-grade materials to choose from, the ProX SLS 6100 brings versatility to your applications, whether for functional prototyping or direct 3D production. Choose from industrial-grade nylon 11 with DuraForm ProX EX BLK or DuraForm ProX PA nylon 12, the flame retardant nylon 12 based powder of DuraForm ProX FR1200, glass-filled DuraForm ProX GF, and aluminum filled DuraForm ProX AF+. DuraForm ProX PA can meet the standards of ISO 10993-5 and 10 opening the door to production of select medical devices.

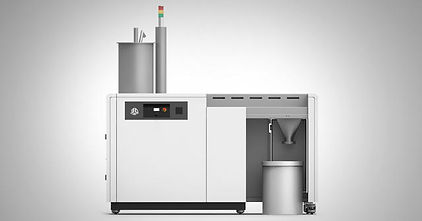
Production Quality, Priced for Prototyping
With automated materials handling through the material quality control (MQC) system, the system provides continuous automatic sifting and filtering while providing maintenance-free transportation of material to the printer. A new air-cooled laser eliminates the need for a chiller, providing greater efficiency and lower total cost of operations. Finished prints feature a smooth surface finish, with the highest resolution and edge definition of any SLS system.
Maximize Your Production with 3D Connect
3D Connect Service provides a secure cloud-based connection to 3D Systems service for preventative support to enable better service, improved uptime and production assurance for your system. Through 3D Connect Manage you can also manage and monitor your equipment with anytime, anywhere access to your print jobs, system performance metrics and usage.


Advance Your Workflow with 3D Sprint
Use this exclusive 3D Systems additive manufacturing software to prepare and optimize CAD data, and manage the SLS printing process. Tools for high-performance, high-density 3D nesting, quality checks for pre-build verification and a sinter cage structure generator bring high performance and productivity to your SLS production process.
APPLICATIONS:
-
Impact resistant, durable prints
-
Engine housings and other protective covers
-
Jigs and fixtures
-
Reduced weight production parts
-
Knobs, handles and other dashboard/interior parts
-
Machinery components
-
Lightweight duct work
-
Small to medium run manufacturing
-
Healthcare device and tools manufacturing
FEATURES:
-
Selective Laser Sintering (SLS) technology
-
Max build envelope capacity
(W x D x H): 15 x 13 x 18 in
(381 x 330 x 460 mm) -
Broad range of production-grade nylon 11, nylon 12 and reinforced materials
-
Consistent mechanical properties
-
High production speed for its class of 2.7 l per hour
-
Streamlined production control, including 3D Sprint™ integrated additive manufacturing software, fully automated powder handling and optional 3D Connect capability
-
Automated 3D part nesting
-
Maximized build volume and density
BENEFITS:
-
Manufacture strong end-use parts and functional prototypes faster
-
Easily print any design without using supports or post processing
-
Integrated printer and material solution with expert application support
-
Full automation of material handling frees valuable resource
-
Streamline your workflow with automated production tools
-
Lower cost of ownership with high throughput and material efficiency
-
Clean 3D printing solution with minimal waste